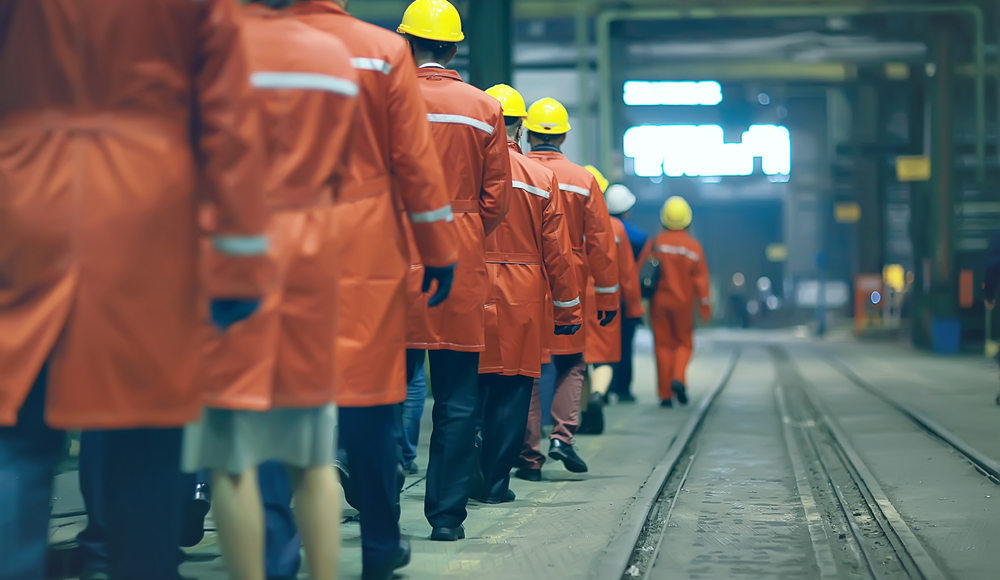
How you can align with Health & Safety legislation updates…
Workforce safety is obviously the top priority for every organisation, particularly those in a notoriously high-risk industry, but alongside safeguarding the workforce there is also a very real threat for every business of incurring heavy fines should accidents occur, or should obvious risks fail to be identified or prevented.
Workplace and site safety can be a challenging enough task, but with recent legislation changes, and likely more to come (in some cases due to Brexit preparations and post-Brexit iterations), the Health & Safety environment potentially becomes more and more of a challenge to maintain compliance.
So what can you do about it?
Firstly, let’s start by painting the picture…
Regulation updates and what seems to many like a much firmer focus from regulatory bodies is very much welcome news, particularly with regards to putting more in place to prevent incidents and keep workers safe. This does however mean businesses are going to need to be more adaptable in order to ensure they can keep up with their part in maintaining effective compliance.
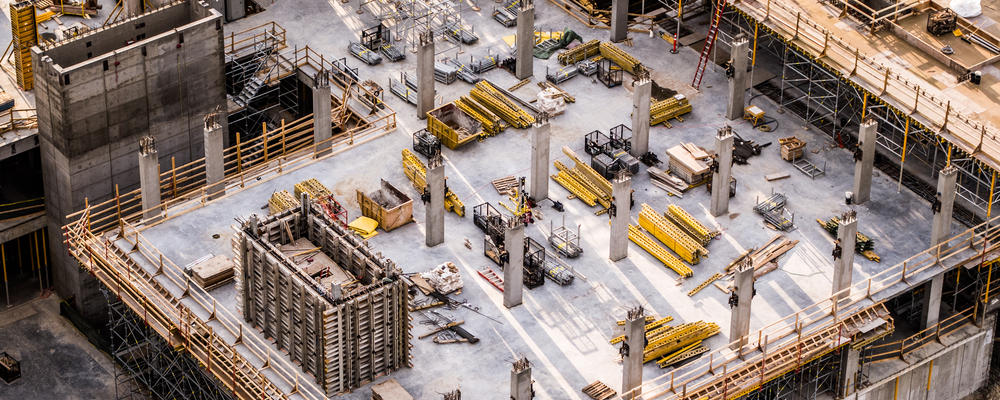
As for why this is happening, we’ve already referenced the effect Brexit has possibly had on transforming Health & Safety legislation into a more fluid environment, but there’s also the statistical factor which is being targeted as an area to improve on…
Looking at UK workplace injury costs alone in 2017/18 (excluding sickness)…
There was a total of £5.2 billion spent in injury costs (source: HSE)
It is predicted that this figure breaks down in the following ways, and when you look into other statistics focusing on the number of injuries you begin to see a picture of how there is room for improvement…
555,000 Non-fatal injuries to workers in 2017/18 (source: Labour Force Survey)
£8,500 estimated average cost per non-fatal injury in 2017/2018 (source: HSE)
144 fatal injuries to workers in 2017/2018 (source: RIDDOR)
So far in 2018/2019 there have been 147 fatal injuries to workers in the UK (source: HSE)
£1.7m estimated average cost per non-fatal injury in 2017/2018 (source: HSE)
These costs are calculated taking ‘everything’ into consideration in-line with the HSE’s ‘Costs to Britain’ ie; loss of production etc.
Greater still, in terms of actual fines incurred for those found guilty of Health & Safety offences in the UK; £71.6 million was issued in 2017/18. The average fine over the course of the year works out at £148,000 per offence where a conviction was secured.
With the vibrancy around Health & Safety law it has never been more important that businesses remain aware of developments. They will need to adapt and train workers accordingly to ensure they don’t add to these statistics.
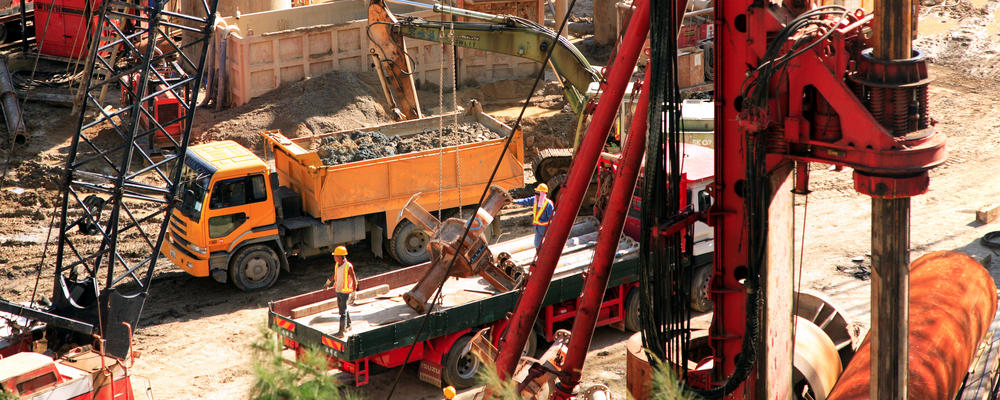
Although worker safety should be the top priority when adapting towards the influx of legislation changes, continued compliance to legislation will be key for any business to avoid regulatory investigation, or worse heavy prosecution.
Some of the most recent identified updates include;
- New guidelines for gross negligence manslaughter
- Higher fines
- Amendments to a host of existing regulations
- Working practice frameworks
In terms of enforcement these updates could potentially send somebody to prison for over a decade, and/or incur a fine that an organisation may not be able to recover from. In terms of support for businesses, initiatives, tools and frameworks are being ever developed to help compliance with standard operating legislation.
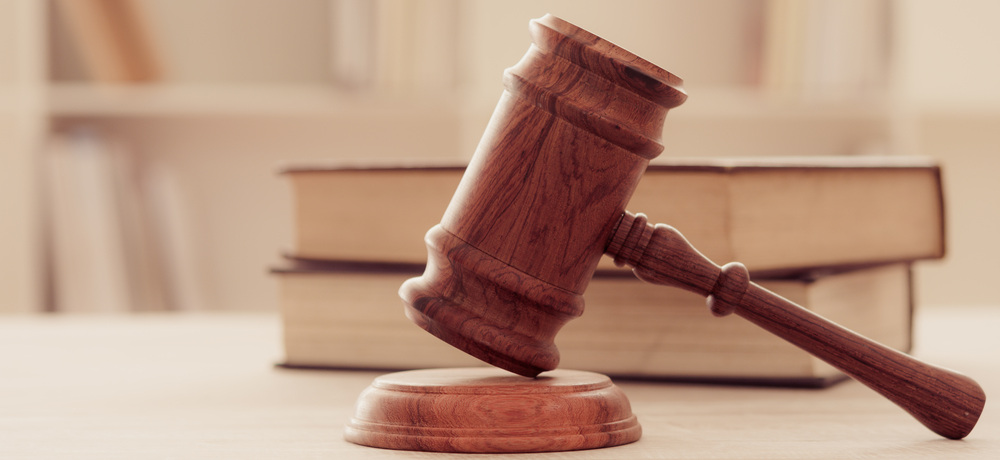
All businesses need to be taking Health & Safety seriously for their workforce safety and for the survival of the organisation. Negligence can lead to life changing/ending incidents and can lead to punishment for a business that can damage beyond repair.
The reasons behind these changes can be seen in the statistics we’ve already witnessed, but the logic behind these changes is clearly around emphasising what more can be done around prevention rather than reaction, and this is exactly how things should be.
The crux of the issue is essentially around ‘optimisation’. With so much going on day to day, with so much that requires attention and awareness, with so much change due over the coming months, with so much greater punishments on the cards and with so much at stake, what can the Health & Safety, or Operations function(s) do to prepare for legislation updates and future changes? How can you streamline processes in-line with the latest legislation so your Health & Safety function can have a greater impact? Ie; so they can provide the care and attention needed in looking forward, ensure the organisation remains compliant and work at building a culture of safety within the organisation. In order to align with Health & Safety legislation updates, quite simply dedicated and effective resource needs to be available to analyse, propose and initiate new measures, counter measures and preventative measures in-line with legislation changes.
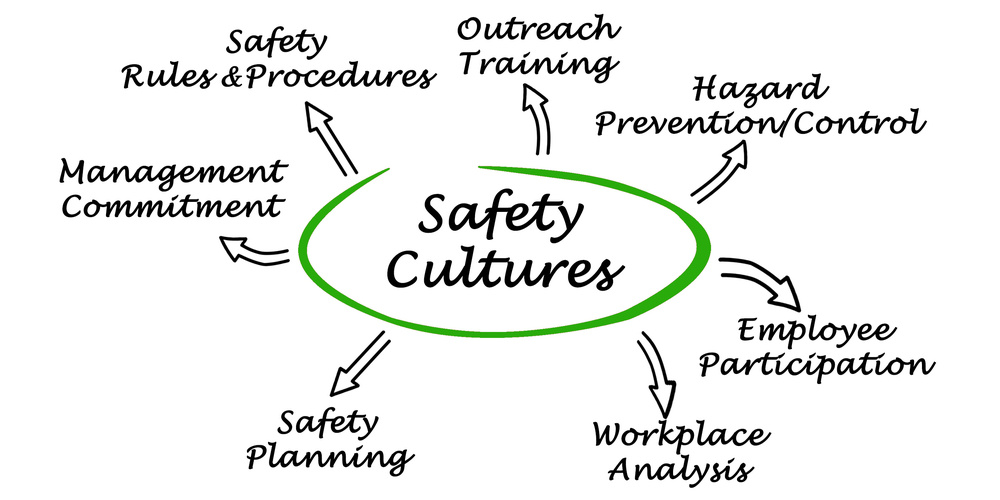
Optimisation, automation and digitisation, innovatively deployed to meet specific and unique business requirements, and aligned to existing business processes can completely remove many of the problems surrounding workforce compliance and competency, allowing your experts to spend their time being experts rather than manually handling monotonous but necessary and important processes…
Using the example of a site induction, how can a Health & Safety function be expected to create a culture of safety, invest their time in the areas that matter the most and look to the future when they are potentially spending up to half their working time manually inducting workers safely onto site? It’s an important part of ensuring workers can perform safely, but does it need to be a resource drain?
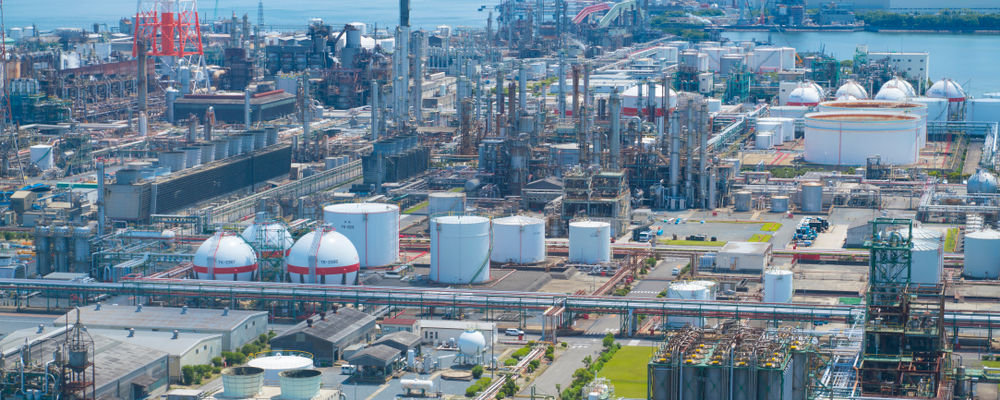
How can your business readily protect itself if a worker is negligent on site? What data do you have available to prove the business has provided all training and information necessary to absolve itself from potential punishment?
How can your organisation prevent incompetent workers coming onto high risk locations? How can it measure the competency of all workers turning up? How can you do all of these things with a workforce of subcontractors not employed by your organisation? How much useful data can you actually gain? How can you gain data without breaching the GDPR? How can the process(es) be streamlined to alleviate workloads?
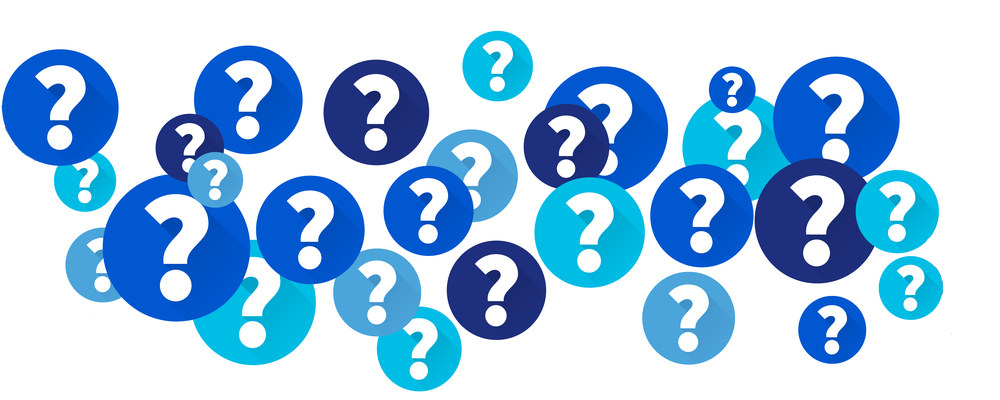
If you opt for a digital solution, how scalable is it? Is it flexible enough to allow you to change things at short notice, say when legislation changes more so in the future and you need to adapt accordingly? How much could you save on operational costs with a digital solution? How much time could you save?
If you’re seeking answers to these questions, or others, there is more than likely a digital solution out there that can help your organisation gear up for the future and meet all internal requirements necessary. Keyzo provides solutions of this nature but delivered through an approach where we sculpt our solutions to provide minimal disruption to your existing processes.
If you’re interested in finding out more, or if you have any concerns about how you can use software to prepare your organisation or your Health & Safety processes for the future, get in touch with Keyzo and we can discuss your needs along with anything you have in mind.
We have two popular Health & Safety centric solutions that can each be configured and managed to work the way you need them to…
Regarding site inductions, site access control, workforce management and proving worker competency we have induct&train.
Regarding notice and policy communications, effective audit trails, streamlining acknowledgement capture and ensuring workforce compliance we have read&sign.